Value Improvement Practices
Project Assurance
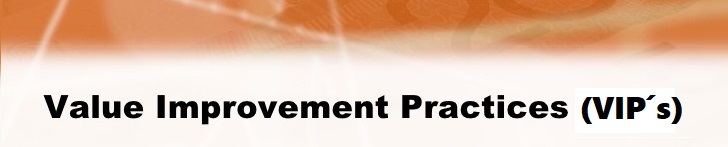
The key purposes of the application of VIP’s during a capital project development and implementation life cycle are: 1. To improve cost performance, 2. To improve schedule performance, 3. To improve the potential for effective operational performance, 4. Contributing to “Best in Class” project performance and 5. Alignment of expectations between stakeholders.
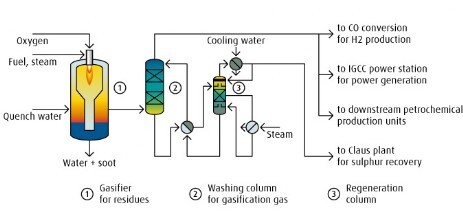
Technology Selection is a systematic process to select the best technology options that meet the project objectives and improve our competitive advantage.
The process of selecting technology is important because it is one of the first activities in the front end loading of a project. At this stage, decisions that are made can have a major impact on the financial success of the project. Technology chosen without a well thought out plan can lead to cost overruns, longer schedules (especially startup), and lost opportunities in the marketplace.
One focus of the process is to search outside sources of technology to break the "not invented here" paradigm. Another vision is to become a "fast follower" in implementing innovative technology.
A key element in this process is to use a multi-functional team to ensure that business, technical, and manufacturing expectations are met. The mix of people also facilitates generating a more all encompassing list of technologies to evaluate. The process can be applied in selecting overall system technology.e.g., FCC Unit or for discrete equipment, e.g., a compressor.
Process Simplification is a structured workshop focused on simplifying development phase, facilities, processing, or equipment requirements while satisfying needed functionality to deliver business outcomes.
It may be applied to new or existing facilities to improve capital, operations and maintenance cost, end-product quality, production capability and flexibility, waste reduction, customer response and inventory reduction. Process simplification focuses on eliminating unnecessary steps and optimizing the number of trains and redundancy allowances, along with operational flexibility. Process simplification is often carried out in conjunction with Design to Capacity.
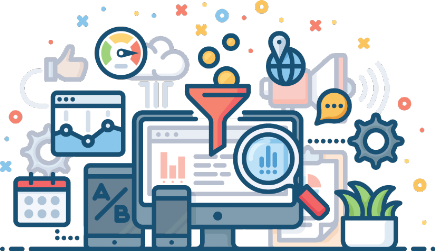
Classes of Plant Quality practice establishes what quality of facility is needed to meet the business goals. It adjusts reliability, expandability, automation, life of the facility, expected stream factor (SF = No. of days plant operates per year/365), likelihood of expansion, production rate changes with time, product quality, and product flexibility. The class of plant quality can be used to determine needed design allowances, redundancy, sparing philosophy and room for expansion.
Waste Minimization is a process stream-by-stream analysis is made to develop concepts and proposals to reduce or better yet eliminate each non-useful stream. This analysis is made before project scope is firm.
Over the past few years, chemical process industries companies have shifted their environmental efforts from controlling discharges after they have been generated to preventing the generation of emissions and wastes in the first place. Emphasis has shifted from end-of-pipe treatment to reduction of wastes at the source, and/or the reuse of wastes as more cost-effective waste management methods. The hierarchy of eliminating or reducing waste can be described as follows:
Prevention:
Waste minimization analysis completed?
Recycle/Reuse:
Can process streams be recycled?
Reduction:
Have waste reduction process options been evaluated?
Treatment:
Minimum essential waste treatm. and disposal methods ID?
This approach has been used successfully in many existing facilities. Unfortunately, it is not always possible to minimize waste at the source or reuse it in an existing facility to the extent that would be desirable. If the physical structure of an existing facility is already in place, this inherently limits the flexibility and options available to reduce or reuse wastes.
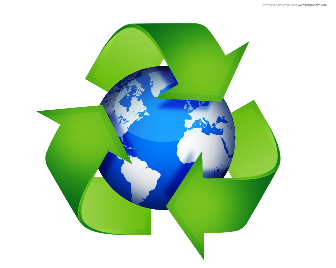
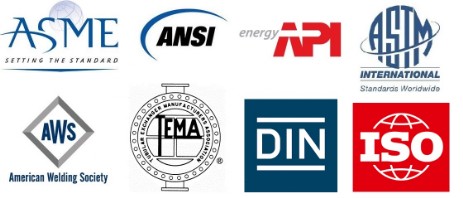
Sometimes the cost of a facility is increased by the application of codes, standards and specifications that exceed the actual needs of the specific facility being designed.
In the early evolutionary days of the chemical industry, uniform design standards were not well defined. As a result, many leading companies developed their own standards based on their internal know-how and experience. Over the years, these standards became rigid and inflexible. In more recent times, design standards have been modernized and accepted broadly across the industry. There are several considerations in deciding what standards and specifications to use on a project. For example, a company's internal standards regarding unique materials of construction for a specific design may be better than a generic, more general standard. However, sometimes the cost of a facility is increased by the application of codes, standards and specifications that exceed the actual needs of the facility being designed. Costs can also be inflated by insistence on unique company standards when acceptable industry standards exist.
Another consideration is the procurement of equipment. A unique process design during early development of a technology often required equipment that was built according to a specific design specification. However, there is no question that procurement of equipment meeting a specific design specification is much more expensive and time-consuming that buying equipment off-the-shelf. This VIP should involve a structured consideration of the needs of the project and selection of the standards and specifications that optimally meet those needs.
Design-to-Capacity evaluates the true required maximum capacity of each major piece of equipment relative to the desired overall facility capacity. Often equipment is designed with a "design factor" which results in larger equipment and some additional capacity. This conservatism can lead to certain equipment or whole plants having overcapacity which the business may or may not want to pay for initially. Excess processing capacity gets incorporated into designs in several ways. The key problem with failing to use a good Design-to-capacity approach is that the excess capacity built into a design inadvertently is always inefficient. As a result, much time later is spent debottlenecking a design that should have either been built for expansion or have been impossible to debottleneck. Design-to-Capacity, as defined here, focuses on:
- Uncertainty in future feed slates
- Physical properties
- Product specifications
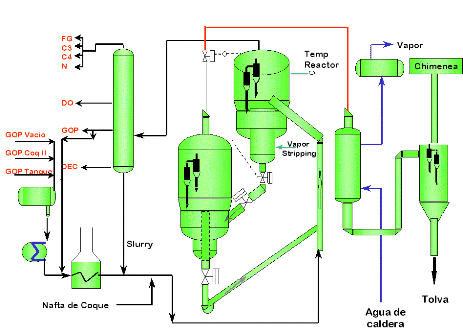
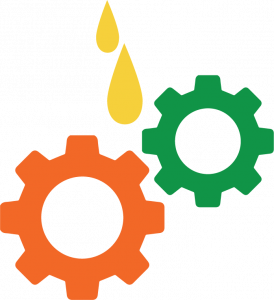
Process Reliability Modeling is a simulation technique to examine operability targets for a facility. Typically, specialized software and/or a consultant is necessary.
Process Reliability Modeling is based on traditional reliability engineering methods.
Whether failures occur or not and their times to occurrence, can seldom be forecast accurately. Reliability is therefore an aspect of engineering uncertainty. Whether an item will work for a particular period is a question which can be answered as a probability. This results in the usual engineering definition of reliability as:
The probability that an item will perform a required function without failure under stated conditions for a stated period of time.
Reliability can also be expressed as the number of failures over a period.
Predictive Maintenance is an approach to maintaining a facility whereby equipment is monitored, and repairs are made before failure. Typically, such an approach requires adding various measurement devices to evaluate operating characteristics.
Traditionally, maintenance engineers have combined many techniques, both quantitative and qualitative, in an effort to predict impending failures and mitigate downtime in their manufacturing facilities. Predictive maintenance offers them the potential to optimize maintenance tasks in real time, maximizing the useful life of their equipment while still avoiding disruption to operations.
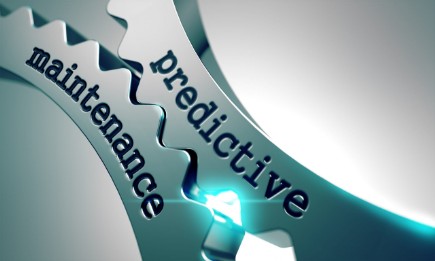
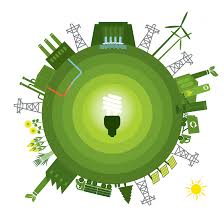
Energy Optimization (EO) is a methodology for optimizing the capital cost, operating cost, and operability of a process unit, utility system, or manufacturing site. Using the basic thermodynamic data for the process(es), targets for energy consumption and power generation that take into account the cost of equipment can be determined.
The purpose of a EO study is to improve the return on investment for projects by identifying the most economical levels of heat recovery and power generation.
A number of Independent Project Analysis (IPA) customers have successfully used EO for debottlenecking process units (retrofits or revamps) constrained by boiler or process heater capacity as well as in optimizing the process designs for grassroots units. The methodology can also be used to optimize site-wide energy usage or to correct energy imbalances on existing sites.
Although an EO is usually associated with energy conservation, it can also lead to reduced capital costs, especially in grassroots process units or sites. This is because the methodology can be used to identify the simplest equipment arrangements out of a range of options having similar operating performance.
Value engineering is a systematic method to improve the "value" of goods or products and services by using an examination of function. Value, as defined, is the ratio of function to cost. Value can therefore be manipulated by either improving the function or reducing the cost. It is a primary tenet of value engineering that basic functions be preserved and not be reduced as a consequence of pursuing value improvements.
For Value Engineering practice one technique that is appropriate for any kind of project as they will allow to place importance on the subjective characteristics and features of alternative systems that are not addressable in terms of pure cost is the Criteria Weighting and Analysis Matrix Techniques.
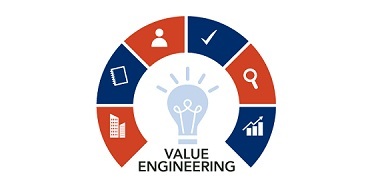
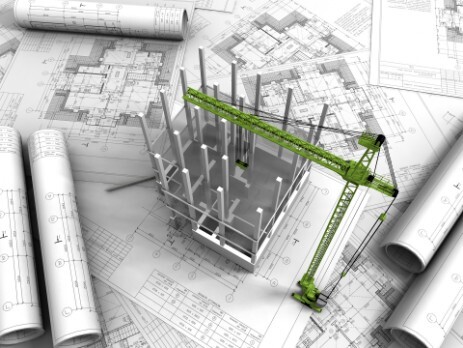
Analysis of the design usually performed by experienced construction team intended to reduce costs or save time in the construction phase
Typically, constructability reviews involve competent construction professionals reviewing the plans and designs after design is essentially complete and resulting changes are minor modifications to ensure feasibility of construction. Even in lieu of a broader program, such reviews can provide significant benefits. However, much greater benefits are obtained when a constructabiliy program involves the construction professionals on a more or less continual basis, beginning at the conceptual stage of the project and continuing through completion of design. In such a program, the construction people function as part of the project design team. As such, they are involved with the total design effort, rather than merely whether a completed design can be readily built or not. They work with the engineers to plan how to best meet the desired end result.
A project utilizing a constructability program changes the focus of engineering planning and scheduling. Engineering and construction work are planned together, with construction needs often driving the engineering approach. This may involve departing from the normal design sequence in order to have engineering deliverables better serve the construction needs. Unusual designs may be needed to allow construction to operate in limited space. Engineering details are designed with the immediate construction input to more closely optimize the project costs. The result in any case is an overall project plan driven by the business needs of the project itself. Engineering schedules are crafted based on a holistic view of the project needs, including optimum construction sequences, as opposed to construction schedules being based on promised drawing issue and material delivery dates.
Properly timed initiation of a constructability program provides early construction sequencing, drawing issue sequence determination, determining the minimum detail work needed to adequately impart the design needs to the construction force, etc. Constructability would ensure site layouts that provide for crane access, adequate laydown space and staging areas, access for materials and personnel, and avoidance of unnecessary limitations on construction methods. Detailed designs would be guided to avoid difficulties in construction.
Life Cycle Engineering Information Management (3D CAD) is the process of managing the entire Engineering Information, through engineering lifecycle.
The management of engineering information (including drawings, documents and data) using computer systems, so that it can be of value throughout the life cycle of the asset, including the project phases, operations and maintenance and final decommissioning and demolition.
Originally, engineering data was relatively simple: design files, parts lists and specifications. At the time, Engineering Data Management Software (EDMS) and later Product Data Management (PDM) allowed users to organize their product data and apply rules for item identification and revision control. An associated electronic data library contained 2D/3D CAD files and other design files.
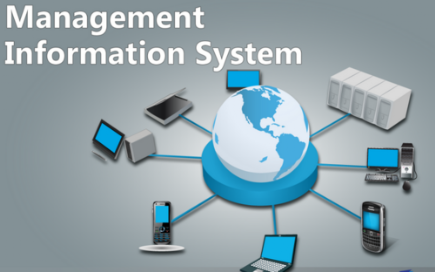